Why should your company be LEAN?
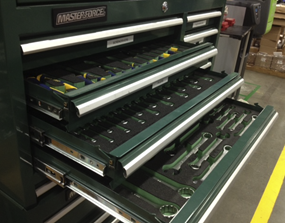
Lean processes, such as the use of shadow boards, can be highly effective in controlling tools in a manufacturing environment.
Implementing Lean processes like shadow boards in a manufacturing environment provides visual organization, standardization, productivity gains, error prevention, safety enhancement, and cost reduction. These benefits make a compelling argument for using Lean methodologies to control tools and optimize manufacturing processes.
Visual Organization
Shadow boards provide a clear visual representation of the tools required for specific tasks. By assigning a designated location for each tool, it becomes easy for workers to identify if any tools are missing or misplaced. This visual organization eliminates waste associated with time spent searching for tools and enhances overall efficiency.
Standardization
Shadow boards promote standardization in tool placement and use. Each tool has a designated spot, and this consistency ensures that everyone knows where to find and return tools. Standardization simplifies training, reduces errors, and minimizes the risk of accidents or damage caused by improper tool use or storage
Improved Productivity
When tools are readily available and organized on shadow boards, employees spend less time searching for them. This leads to improved productivity as workers can quickly locate and retrieve the required tools. Reduced search time translates to more time spent on value-adding activities, thereby increasing overall output.
Visual Control
Shadow boards offer a visual control mechanism for monitoring tool inventory. By glancing at the board, supervisors and employees can easily identify which tools are missing or in use. This enables timely replenishment and prevents production delays or downtime caused by unavailable tools.
Error Prevention
Shadow boards can help prevent errors by visually indicating when a tool is missing or misplaced. If a tool is absent from its designated spot, it serves as an immediate visual cue that something is amiss. This prompts workers to investigate and rectify the situation promptly, reducing the chances of using the wrong tool or creating defects in the manufacturing process.
Safety Enhancement
Organized tools contribute to a safer work environment. Shadow boards promote proper tool storage and reduce the risk of accidents caused by loose or improperly stored tools. By adhering to Lean principles, manufacturing facilities can create a culture of safety and ensure compliance with safety regulations.
Cost Reduction
Lean processes, such as shadow boards, can lead to cost savings in several ways. By preventing tool loss or damage, organizations can avoid unnecessary expenditures on tool replacement. Moreover, the improved efficiency and productivity resulting from a well-organized tool control system can lead to reduced labor costs and increased output without additional resources.
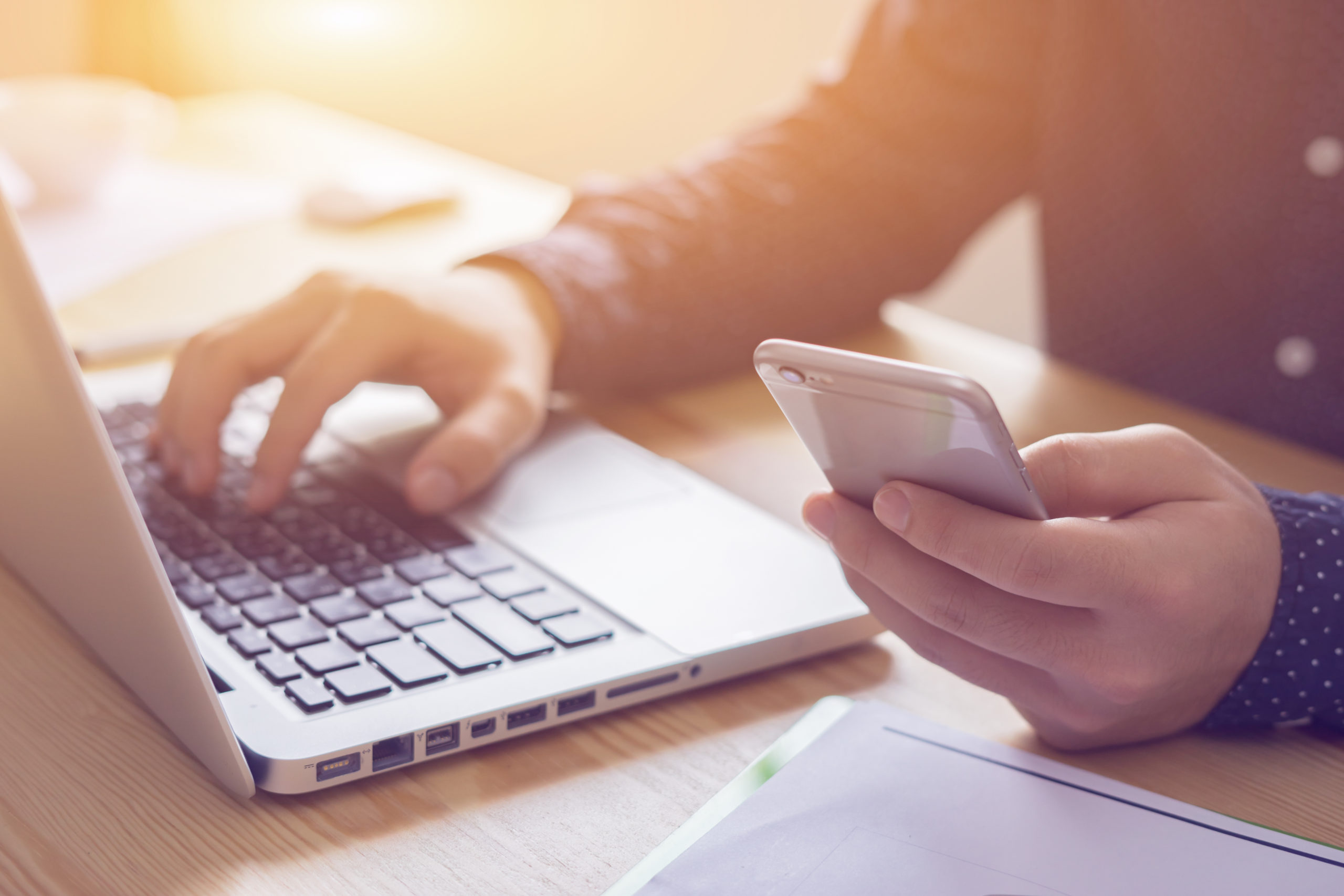
Return on Investment (ROI)
Calculation for implementing Lean processes like shadow boards in a manufacturing environment:
- Cost of Implementation:
- Cost of shadow board materials (e.g., boards, hooks, labels)
- Cost of labor for designing and implementing the shadow board system
- Cost of training employees on the new system
- Cost Savings and Benefits:
- Reduced tool search time: Calculate the average time employees spend searching for tools before and after implementing shadow boards. Multiply the time saved per employee by their hourly wage rate.
- Increased productivity: Determine the increase in output or number of units produced per hour or per shift as a result of reduced tool search time and improved organization. Multiply the increase in output by the unit price or value per unit.
- Error prevention: Estimate the cost savings from preventing errors, defects, or accidents that may occur due to missing or improperly used tools. This can include potential scrap costs, rework costs, or costs associated with safety incidents.
- Reduced tool loss and damage: Estimate the cost savings from minimizing tool loss or damage due to improved organization and accountability.
- Calculate the ROI:
- Subtract the total cost of implementation (Step 1) from the total cost savings and benefits (Step 2).
- Divide the net cost savings by the cost of implementation.
- Multiply the result by 100 to express the ROI as a percentage.
For example:
Total Cost of Implementation = $5,000 Total Cost Savings and Benefits = $15,000 Net Cost Savings = $15,000 – $5,000 = $10,000 ROI = ($10,000 / $5,000) x 100 = 200%
In this example, the ROI for implementing shadow boards would be 200%, indicating that the benefits and cost savings from reduced tool search time, increased productivity, error prevention, and tool loss reduction outweigh the initial implementation costs by a factor of two.
Note that the ROI will vary based on the specific circumstances, costs, and benefits in your manufacturing environment. It’s important to gather accurate data and tailor the calculation to your organization’s situation for a more precise evaluation.