OSAAP’s Innovative Process: Enhancing Efficiency and Traceability in Aircraft and Aerospace Manufacturing
In the highly regulated and precision-driven fields of aircraft and aerospace manufacturing, the organization and management of tools are critical to ensuring safety, efficiency, and compliance. OSAAP’s process offers an innovative solution that streamlines the creation and management of custom shadow board inlays, specifically designed to meet the unique needs of these industries.
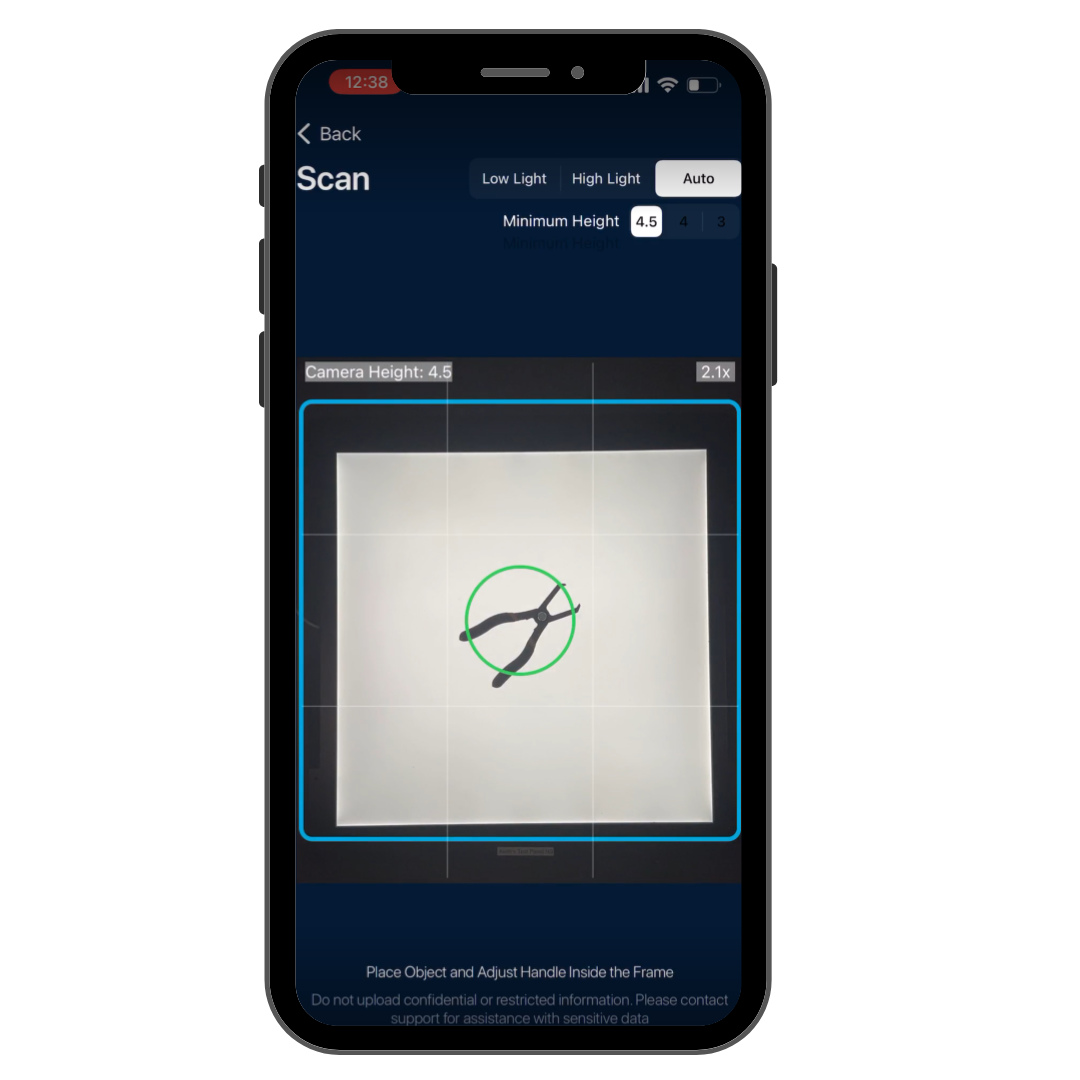
Seamless Integration of 3D Scanning and CAD Software
OSAAP’s process begins with the ability to scan tools directly, capturing their exact dimensions and shapes. This scanned data is then imported into user-friendly CAD software, where it can be used to create custom foam and plastic shadow board inlays. These inlays are essential for organizing tools in a way that maximizes efficiency, reduces the risk of tool loss, and ensures that everything is easily accessible and accounted for.
This seamless integration of 3D scanning and CAD software allows manufacturing facilities to quickly and accurately design layouts tailored to their specific needs. Whether it’s for standard tools or specialized equipment unique to aerospace applications, the ability to customize shadow board inlays ensures that every tool has its designated place, reducing downtime and increasing operational efficiency.

Comprehensive Project Database with Full Backward Traceability
A standout feature of OSAAP’s process is the management of designs within a robust project database. This database not only stores all design files but also provides full backward traceability, allowing manufacturers to track the history of each shadow board inlay. This is particularly valuable in aerospace manufacturing, where stringent quality control and documentation are required.
The traceability feature ensures that any changes or updates to tool layouts can be tracked and audited, providing confidence that all processes adhere to industry standards and regulatory requirements. This level of documentation is crucial for compliance with aerospace regulations and for maintaining high standards of quality and safety.
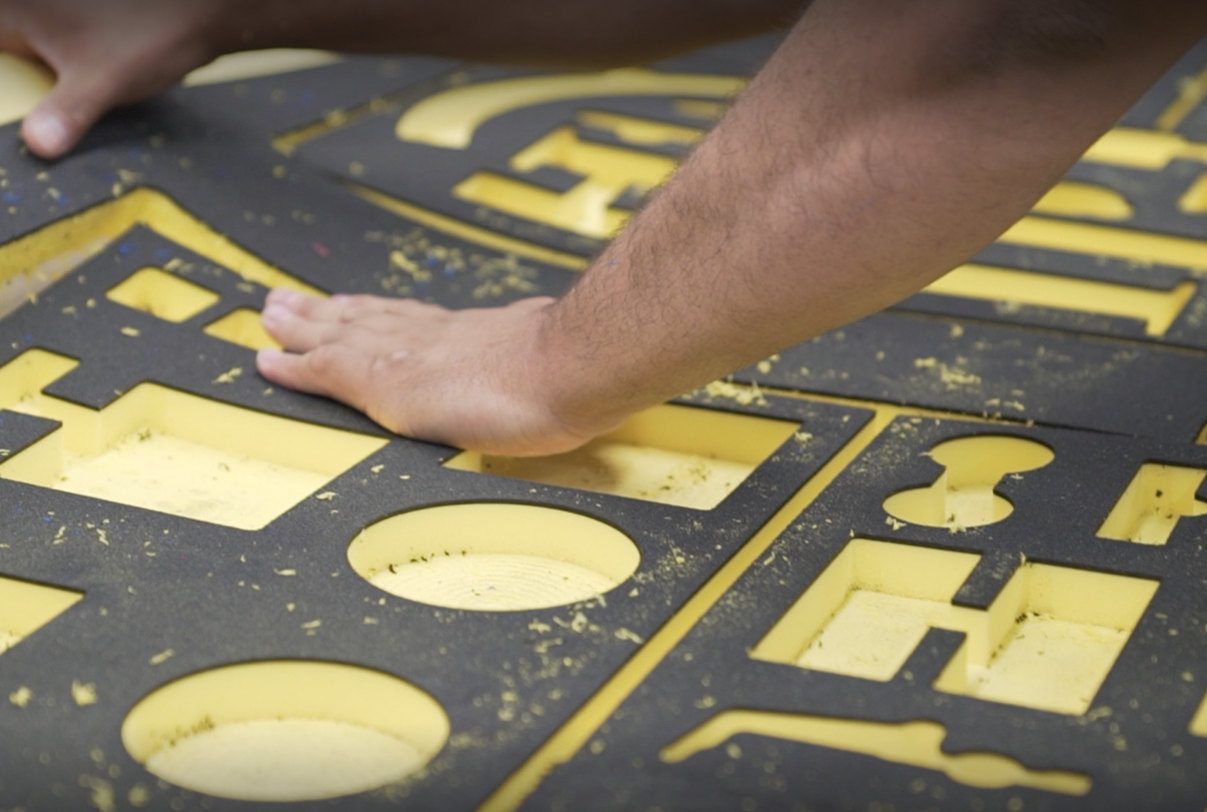
Flexible Production Options: In-House or Through OSAAP
Manufacturers have the flexibility to choose how they want to produce these custom shadow board inlays. They can order the inlays directly from OSAAP, taking advantage of the company’s expertise and advanced manufacturing capabilities. Alternatively, manufacturers can bring the OSAAP process in-house, allowing them to produce shadow board inlays onsite.
Bringing the process in-house offers several advantages, including faster turnaround times, greater control over the manufacturing process, and the ability to make adjustments on the fly. This flexibility is particularly beneficial in the fast-paced aerospace industry, where the ability to quickly adapt to changing needs and requirements is essential.
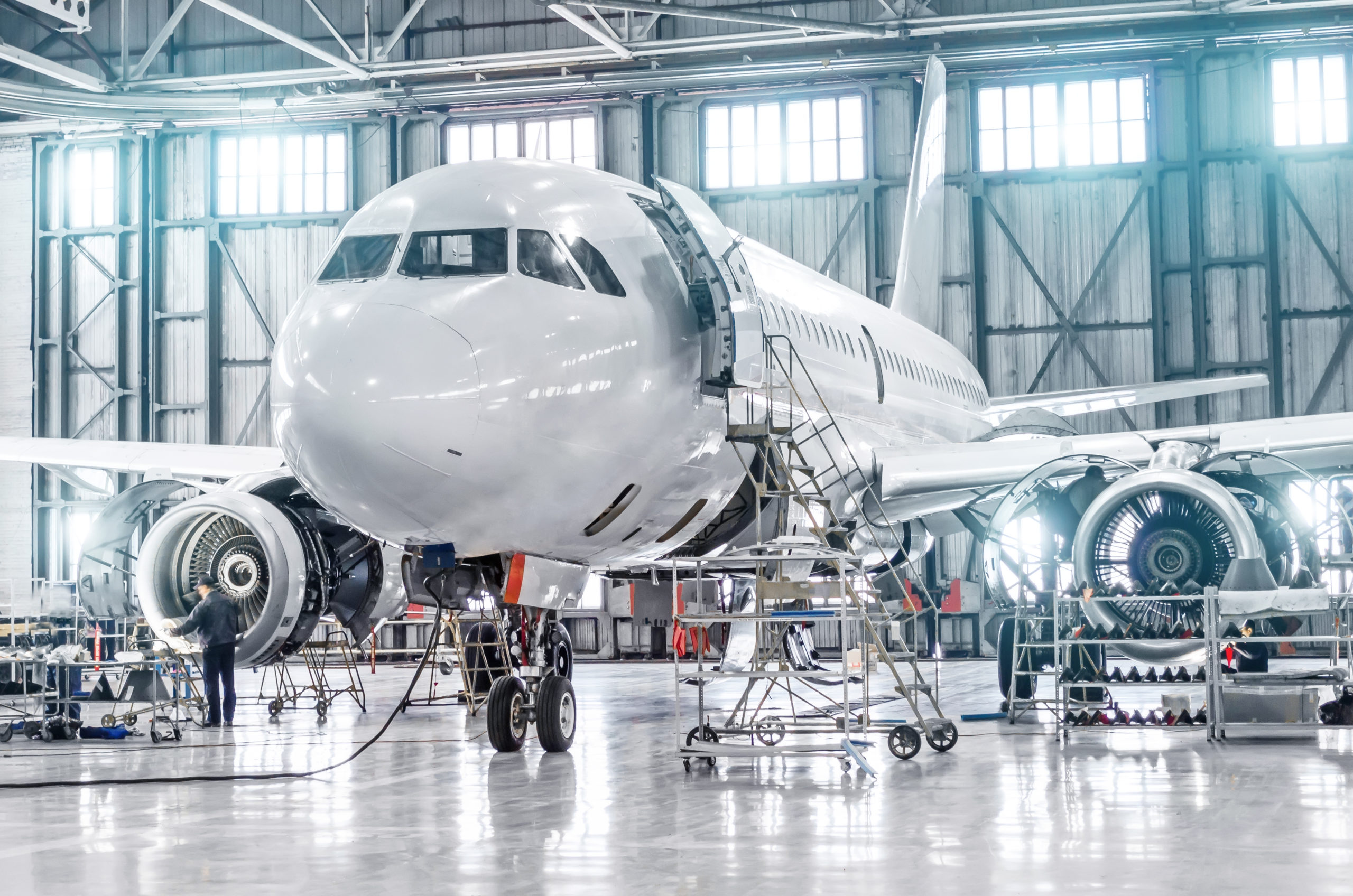
Enhancing Tool Management and Operational Efficiency
OSAAP’s process represents a significant advancement in tool management for aircraft and aerospace manufacturing facilities. By enabling the easy creation of custom shadow board inlays through 3D scanning and CAD software, and by offering a project database with full traceability, OSAAP helps manufacturers achieve greater efficiency, organization, and compliance. Whether through in-house production or orders placed directly with OSAAP, this process provides a tailored solution that meets the exacting standards of the aerospace industry.
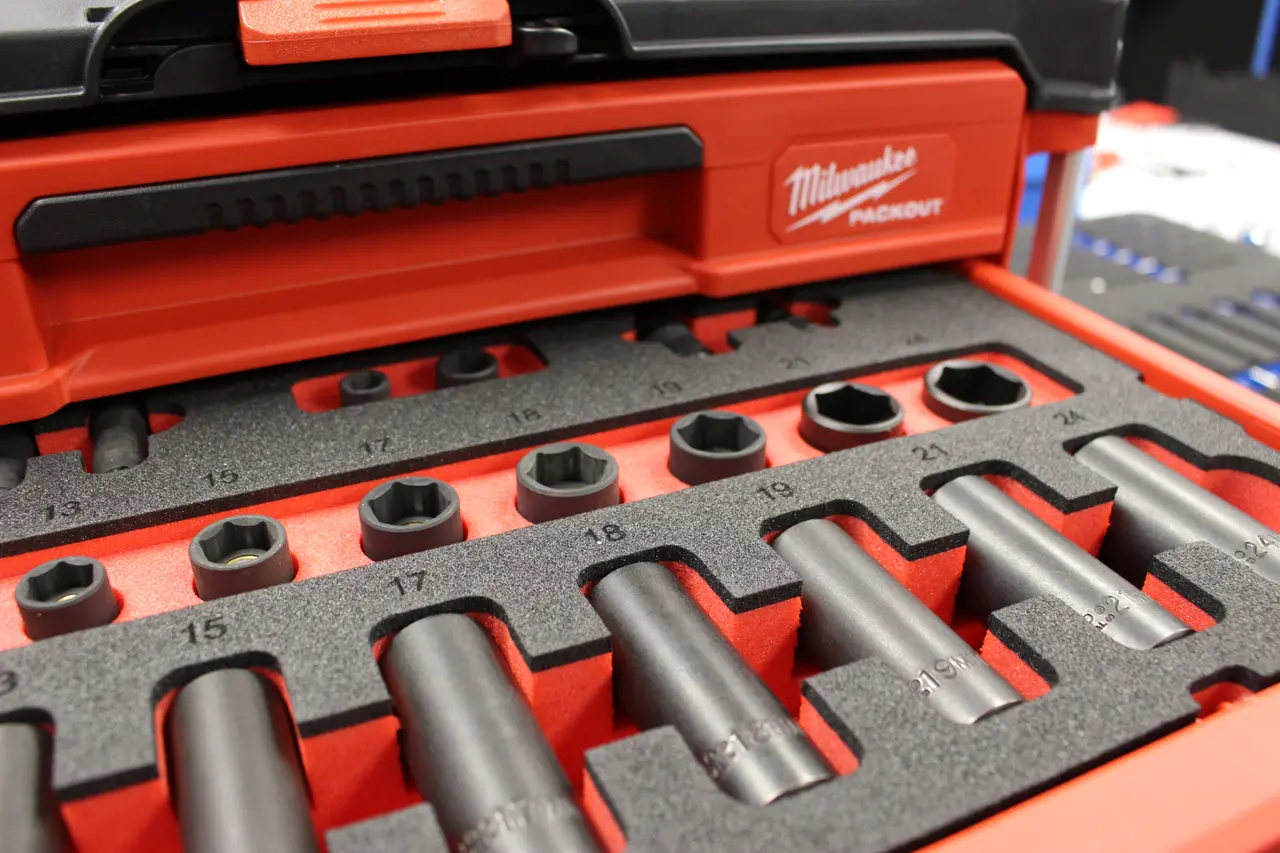
FOD Control
FOD control is a critical part of aircraft and aerospace manufacturing. Every tool used in the manufacturing process needs to be identified before an aircraft engine or rocket can move from one step of the assembly operation to the next. Every part used in the assembly of the aircraft or rocket needs to be safely stored and accounted for. Each tool and part used is unique and requires it’s own unique storage location.
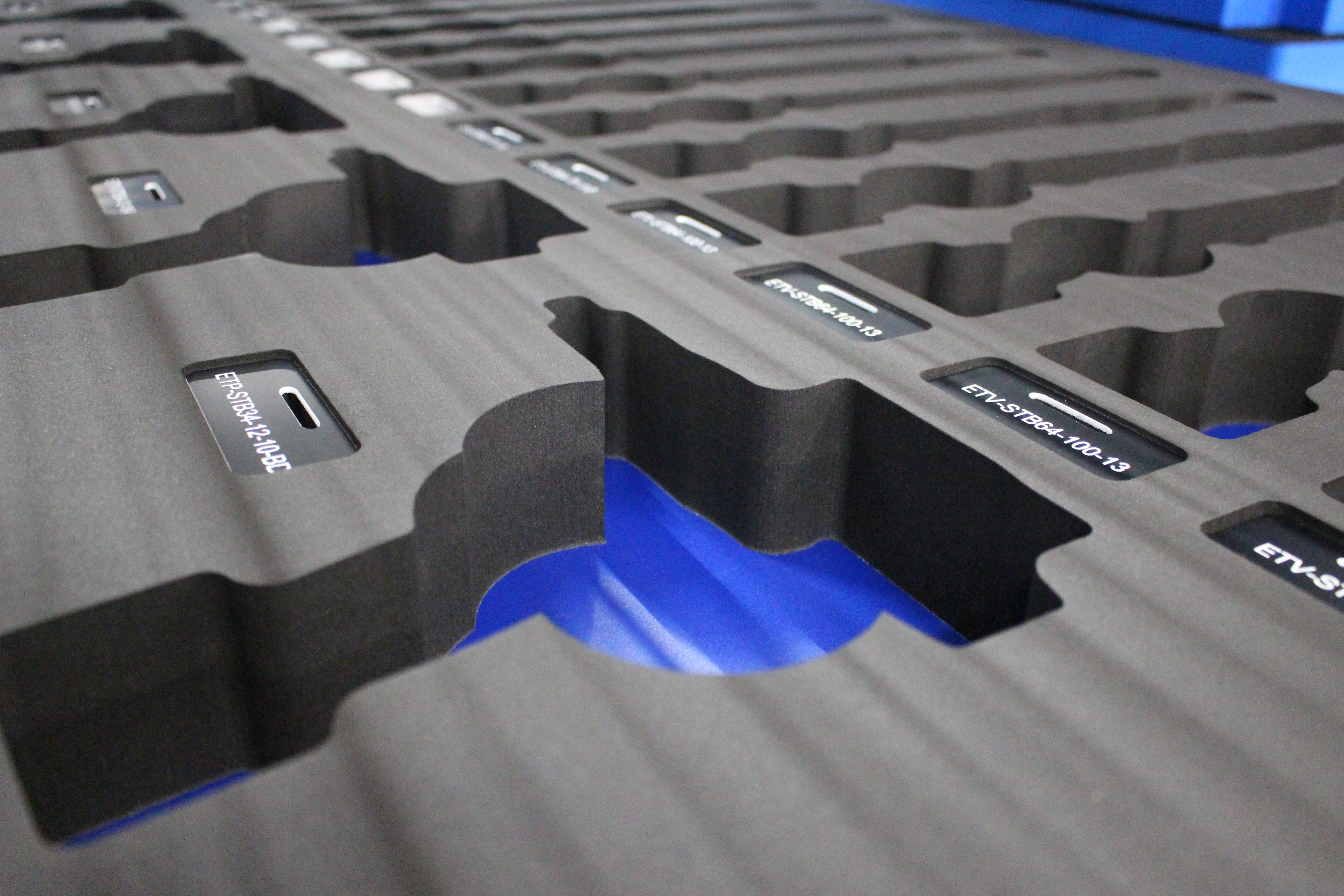
ITAR Compliance
In environments where security is paramount, such as ITAR (International Traffic in Arms Regulations) facilities, maintaining the integrity of sensitive designs and data is critical. These facilities are designed to handle restricted information related to defense and military technologies, where strict controls are enforced to prevent unauthorized access and export.
One significant advantage of ITAR-compliant facilities is their capability to operate entirely disconnected from the internet. This isolation ensures that design data remains secure, protecting it from potential cyber threats and unauthorized breaches. By keeping the manufacturing process within a controlled, offline environment, sensitive information never has to leave the secure facility.
The OSAAP Blue Mill, an advanced CNC milling machine, plays a key role in this secure workflow. Within the ITAR facility, design files can be converted onsite into NC (Numerical Control) code, which the Blue Mill uses to execute precise machining tasks. The ability to perform this conversion and production entirely within a secure environment is crucial for industries where data security is non-negotiable.